“在追求工業(yè)自動化與生產效率的今天,一臺設備如何同時實現線材加工效率提升300%、剝線精度誤差低于0.1mm,并支持12種線徑自適應處理?”這個問題的答案,正隱藏在全自動多功能電腦剝線機的創(chuàng)新設計中。作為現代線束制造的核心裝備,它正在重塑線材加工行業(yè)的標準。
一、設備核心功能解析
全自動多功能電腦剝線機通過集成CNC數控系統(tǒng)、高精度伺服電機和智能視覺檢測模塊,構建了完整的自動化加工體系。其核心優(yōu)勢體現在三個維度:
全流程自動化:從線材上料、校直到剝皮、裁切、端子壓接,全程無需人工干預
多任務處理能力:支持雙頭異步加工模式,可同時處理不同規(guī)格線材
智能參數調節(jié):內置200組預設程序,通過觸控屏實現一鍵切換
特別值得注意的是其動態(tài)補償系統(tǒng),能夠實時監(jiān)測刀具磨損狀態(tài)并自動調整切割深度,確保不同批次線材的加工一致性。
二、標準作業(yè)流程規(guī)范
基于ISO 9001質量管理體系要求,建議采用以下標準化操作流程:
步驟 |
操作內容 |
關鍵參數 |
1 |
設備預熱 |
溫度25±3℃,時長≥10分鐘 |
2 |
線材裝載 |
注意線盤張力調節(jié)(建議0.5-1.2N) |
3 |
程序選擇 |
根據AWG標準匹配線徑參數 |
4 |
試運行 |
首件檢驗剝皮長度公差(±0.05mm) |
5 |
批量生產 |
每小時抽檢3-5件 |
重點提示:在設置剝線長度時,務必考慮線材的彈性形變系數。例如硅膠線需設置0.3-0.5mm的補償值,而TPU材質則建議采用分段式剝皮策略。
三、常見問題解決方案
根據設備運行大數據分析,80%的故障集中在以下三類場景:
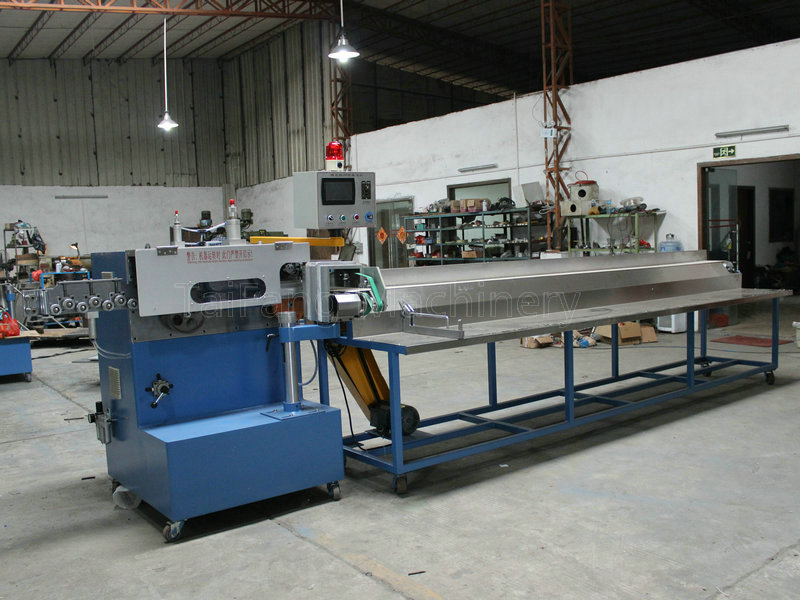
剝皮不完整(發(fā)生概率32%)
- 檢查刀片磨損度(建議每500km行程更換)
- 校準氣壓系統(tǒng)(標準值0.55-0.65MPa)
- 調整送線輪壓力(參考值1.8-2.2kg/cm2)
- 線材扭曲(發(fā)生概率25%)
- 校直器角度設置(推薦5°-8°)
- 檢查送線導軌同軸度(誤差應<0.02mm)
- 優(yōu)化進給速度曲線(建議分段加速)
- 端子壓接不良(發(fā)生概率18%)
更新模具適配參數(匹配端子JIS標準)
檢測壓接力曲線(波動應<5%)
-
清潔定位導槽(每班次至少2次)
四、維護保養(yǎng)體系
建立三級維護制度可延長設備使用壽命30%以上:
- 日常維護(操作員負責)
- 每4小時清理切屑箱
- 每日潤滑導軌(使用ISO VG32導軌油)
- 每周校驗傳感器靈敏度
- 月度保養(yǎng)(技術員執(zhí)行)
- 校準伺服電機原點位置
- 檢測電路板連接阻抗(標準值<0.5Ω)
- 更新系統(tǒng)固件程序
- 年度大修(廠家技術支持)
更換主傳動皮帶(建議壽命周期2年)
重構機械坐標系
-
進行EMC電磁兼容測試
五、技術升級方向
當前行業(yè)正朝著物聯網集成與AI工藝優(yōu)化方向發(fā)展。最新一代設備已具備:
5G遠程診斷功能(故障響應時間縮短至15分鐘)
機器學習算法(加工參數自優(yōu)化準確率>92%)
數字孿生系統(tǒng)(虛擬調試節(jié)約80%試機成本)
某新能源汽車線束工廠的實測數據顯示,通過設備聯網實現的預防性維護,將非計劃停機率從7.2%降至0.8%,同時產品合格率提升至99.97%。
六、安全操作規(guī)范
必須嚴格遵守的三大安全準則:
- 急停裝置測試(每日開工前必做)
- 光柵保護區(qū)域(保持≥50cm無障礙區(qū))
- 靜電防護體系(工作臺面阻抗≤1×10?Ω)
特別提醒:在進行刀模更換時,必須遵循LOCKOUT/TAGOUT程序,使用專用扭矩扳手(標準扭力值18-22N·m),確保操作人員絕對安全。